
-
Strengthening Quality Management in a Mid-Sized Pharmaceutical Company Through Staff Augmentation
Background
A mid-sized pharmaceutical company was struggling to maintain a strong Quality Management System (QMS) due to limited in-house expertise and an evolving organizational structure. As regulatory compliance became increasingly complex, internal teams found it challenging to align quality processes across manufacturing, clinical, and toxicology departments.
Recognizing the need for specialized support, the company sought strategic staff augmentation to strengthen its quality management framework.
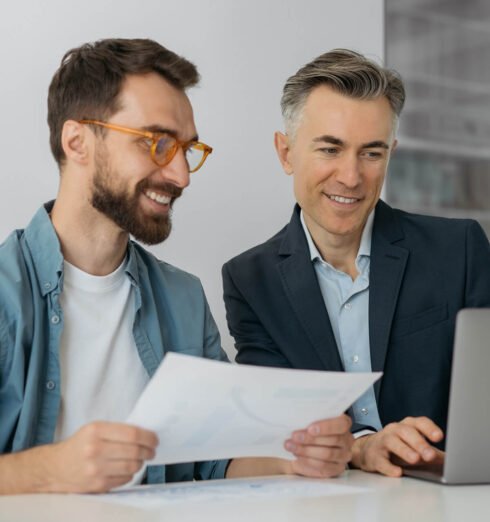

Challenges
1. Gaps in Quality Management
Existing quality processes lacked uniformity across departments, increasing the risk of compliance issues. The company needed expert guidance to identify and address these gaps.
2. Transitioning to a Scalable System
With plans for expansion, the company required a comprehensive transition plan to ensure that its quality systems could grow seamlessly while remaining compliant with industry regulations.
3. Cross-Departmental Integration
Different teams were operating in silos, leading to inconsistent quality practices. A structured approach was required to streamline and integrate quality standards across the organization.
Solution: A Strategic Quality Lead Placement
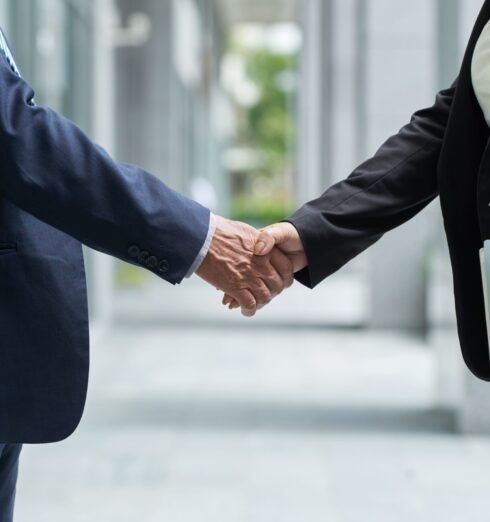
To address these challenges, the company partnered with an experienced pharmaceutical staffing and consulting firm to augment its quality team. The firm provided a seasoned Quality Lead with deep expertise in regulatory compliance, quality systems, and cross-functional integration.
Phase 1: Rapid Gap Assessment
- The consultant conducted a thorough review of the company’s existing quality processes.
- Key compliance gaps were identified, and a structured remediation plan was created.
Phase 2: Developing a Scalable Transition Plan
- A roadmap was designed to ensure seamless quality system expansion as the company grew.
- Best practices were implemented to meet stringent FDA and global regulatory requirements.
Phase 3: Implementing Quality System Integration
- The consultant worked closely with manufacturing, clinical, and toxicology teams to ensure alignment.
- Clear standard operating procedures (SOPs) and training programs were introduced to create consistency.
Results & Impact
✔ Stronger Quality Compliance: The company’s QMS was fully aligned with FDA and global standards, reducing regulatory risks.
✔ Seamless Integration: Quality processes were standardized across all departments, eliminating silos and improving efficiency.
✔ Scalable Growth: The newly implemented system allowed the company to expand operations smoothly without quality bottlenecks.
✔ Long-Term Success: The consultant’s role evolved into a full-time leadership position, ensuring continuity and ongoing improvements.
Conclusion
By leveraging strategic staff augmentation, this mid-sized pharmaceutical company successfully transformed its quality management processes. The expert placement not only ensured compliance but also laid the foundation for sustainable growth.
This case highlights how the right talent at the right time can make all the difference in achieving regulatory excellence and operational efficiency in the pharmaceutical industry.